Meet Me: A New Approach to Automating Order Fulfillment
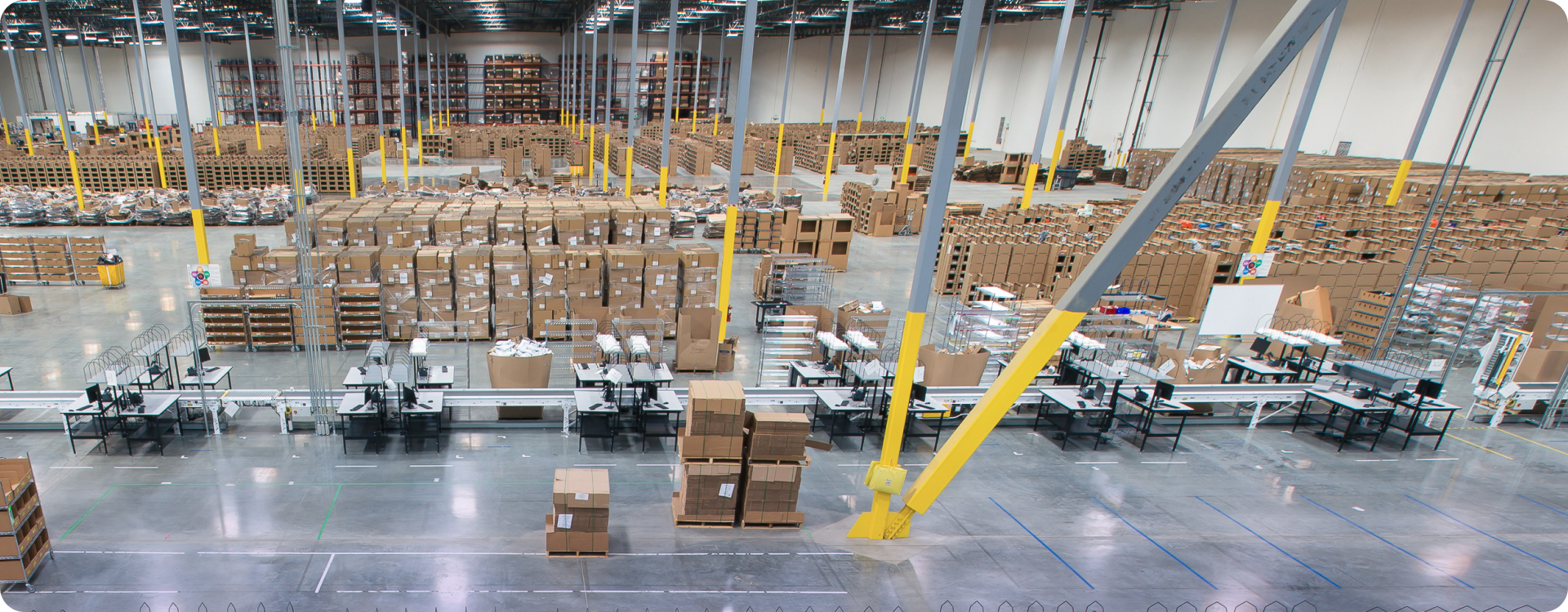
When investing resources and time into selecting and implementing an order fulfillment automation solution, it’s important to understand and evaluate which autonomous mobile robot (AMR) system approach aligns to your organization’s KPIs, supports your workforce, and enables your operations to meet service level agreements (SLAs) and keep up with demand.
In fulfillment warehouses, talent is scarce and resources are tight, yet customer expectations remain high. As supply chain leaders look to do more with less, automating traditionally manual processes has shifted from a “nice-to-have” to a “must-have,” safeguarding warehouses from ongoing labor challenges and variations in customer demand. The order-picking process is widely reported as one of the most costly and resource-heavy processes within a fulfillment warehouse.
Current mobile robotic solutions on the market offer various methods to coordinate and connect human and robotic workforces for order picking. However, gaps remain in implementing technology that reduces warehouse manager and picker effort as well as click-to-customer turnaround time.
Why Order Picking Automation
Ongoing labor challenges and unpredictable swings in demand have warehouse and distribution center managers looking for flexible and easy-to-implement automated solutions. In Instawork’s annual state of the warehouse report, 64% of respondents said they had to forgo business worth more than 25% of their revenue in 2022 because of staffing issues1.
64%
of survey respondents had to give up revenue that amounted to more than 25% of their business due to staffing challenges in 2022.
SOURCE: Instawork State of Warehouse Labor
Warehouse jobs boomed with e-commerce growth during the pandemic, but now leaders are shifting investment to automate processes to reduce costs and increase productivity. With temporary or flexible workers in the warehouse on the rise and layoffs affecting full-time workers across the industry, relying solely on manual labor to keep up in an on-demand market is no longer a sustainable or dependable strategy.
As supply chain leaders search for opportunities to increase margins and grow revenue, identifying operational processes to automate that boost productivity while reducing costs will have the most impact. What activities are most critical in meeting customer expectations and budget? In Peerless Research Group’s 2023 Automation Study, picking efficiency (lines picked per hour) was reported as the top area for improvement in warehouse and distribution center operations over the next two years2. In end-to-end fulfillment processes, accuracy and speed are key to successfully meeting SLAs.
Introducing robotics can optimize the picking process, significantly reducing worker travel and errors while providing the agility to adapt when swings in demand occur.
Order picking is widely reported to account for 50% to 55% of total warehouse operational costs.
As robotic technology continues to evolve, it remains a partially manual process to fulfill customer orders. Therefore, when automating order picking, it is not simply automating manual tasks and determining the proper picking method, but orchestrating and optimizing how human workers and AMRs work together. How workflows are assigned, orchestrated, and communicated across resources is critical to increasing uptime and pick rates. This is where various AMR system vendors used in warehouses and distribution centers (DCs) begin to differ.
Connecting and Coordinating Resources
With humans and robots working together, task assignment, labor balancing, and communication are key to executing efficient and seamless workflows. Legacy person-to-goods AMR warehouse systems have traditionally offered two worker/robot workflow orchestration models: “follow me” and “find me.”
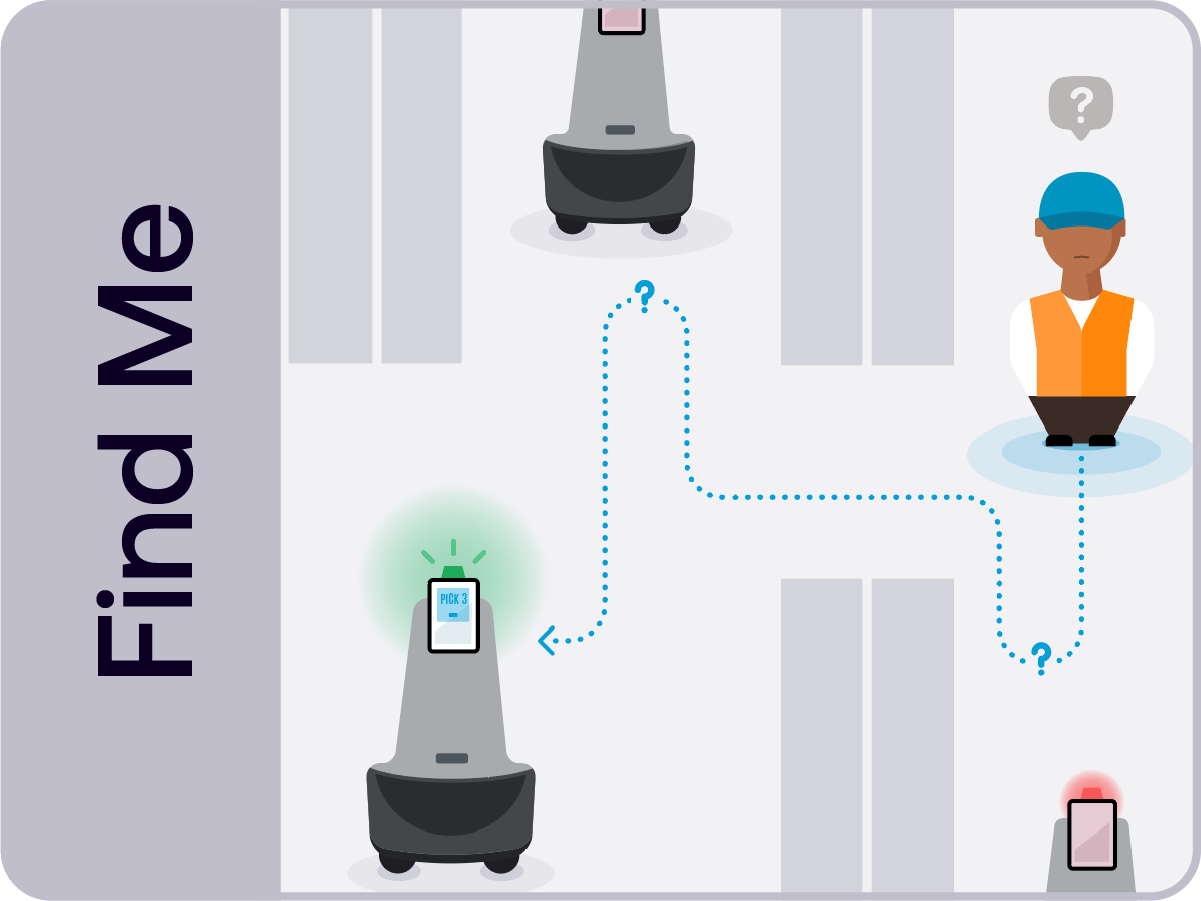
Approach 1: Find Me
In the “find me” or swarm model, many robots roam a zoned area. Pickers are required to find and select a robot that has work available, typically indicated by a flashing light or color on the tablet attached to the robot. In both models, human workers are dependent on robots to initiate and complete picks. Operations managers must also ensure proper people zoning and management to prevent downtime and maximize resources. Maintaining and increasing productivity can be challenging if work isn’t continually monitored and allocated properly across all zones and robots.
Approach 2: Follow Me
The “follow me” model of some AMR solutions requires the picker to follow the robot in order to complete picks. The picker is directed by the user interface on the tablet mounted on the robot for pick location and instructions. Pickers are assigned to one robot, and their picking speed is limited by the speed of that robot. Picking speed is also sometimes affected by the mounted tablet: if pickers forget what they need to pick or how many, they may need to walk around the robot to confirm the information.
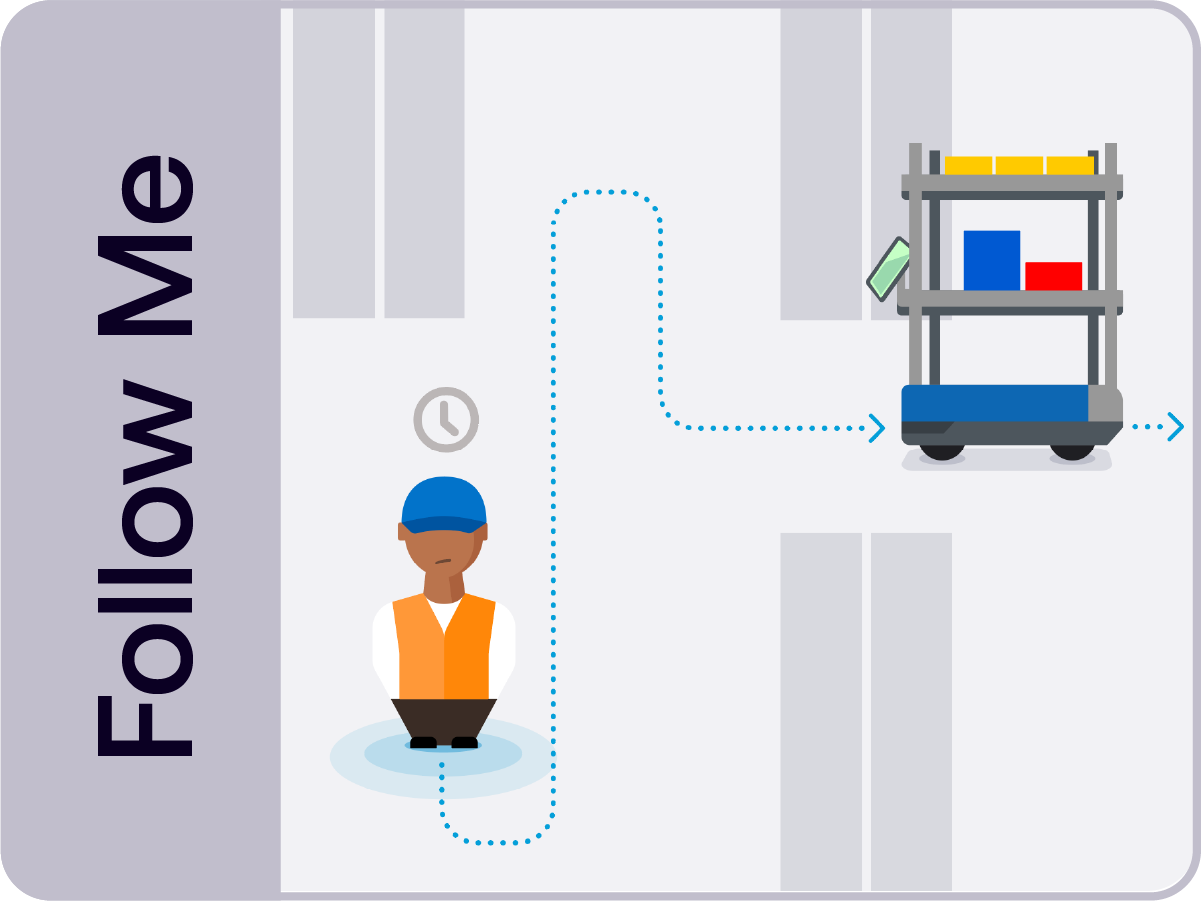
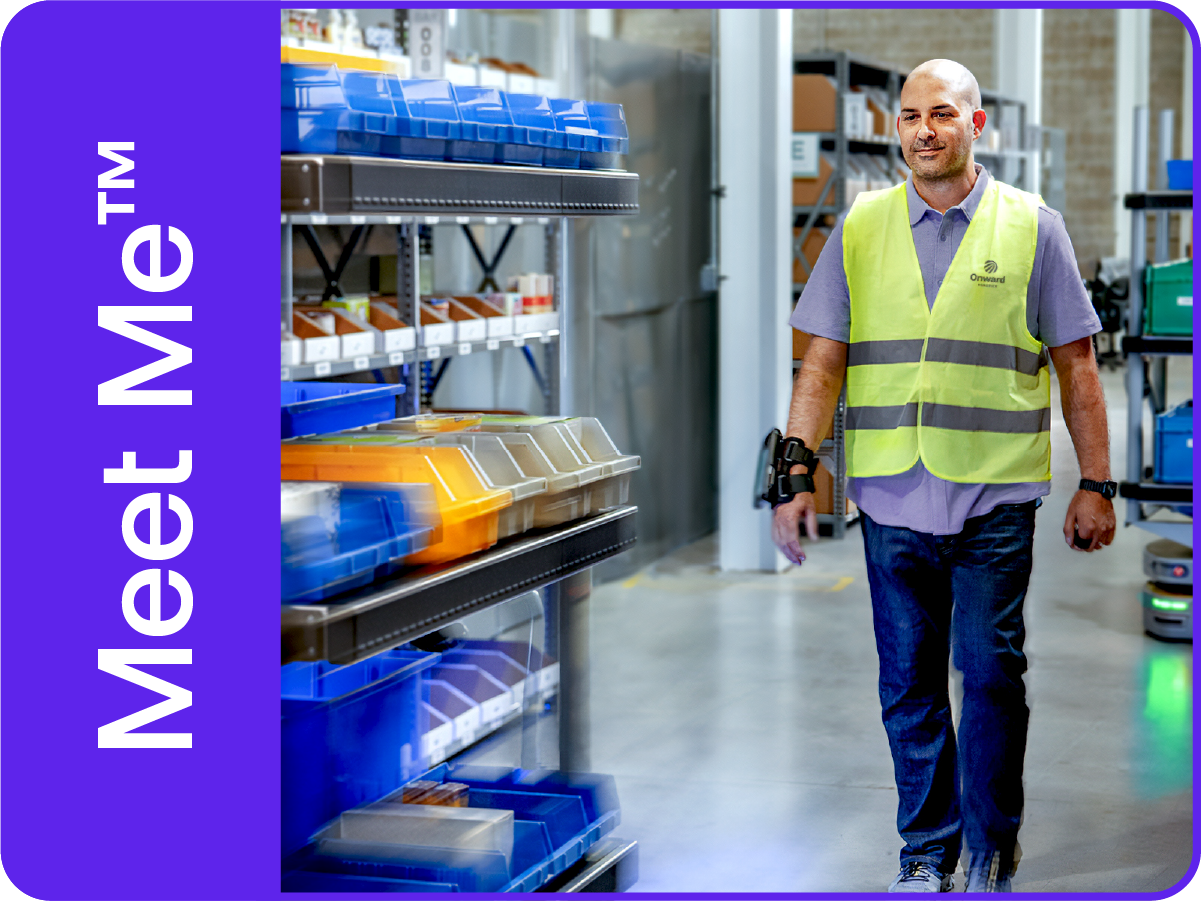
Approach 3: Meet Me™
Onward Robotics’ Meet Me model is driven by Pyxis™ technology that orchestrates humans and robots separately in their own directed workflows. In this unique model, pickers are empowered with the information they need using the Pyxis Point mobile app. They can move independently, meeting their robotic counterparts at the pick location. Since pickers don’t need to rely on robots for directions or pick information, downtime spent waiting on or finding a robot is eliminated. Warehouse managers also save time without the need to plan or coordinate human and robot resources.
Pyxis technology-directed task assignment and labor balancing are catered to each customer’s operational needs. Resources are prioritized and planned based on distance, priority of orders, and robot dwell time for continuous and fast fulfillment. Since both individual workflows are optimized, this innovative approach doesn’t require a swarm of robots or additional travel by the picker to maintain productivity.
Working Better Together
Orchestration of resources optimizes workflows, however, successful implementation, adoption, and ongoing usage of robotic automation also relies on optimal human and robot interaction. Workers filling these roles continue to change, with 69% of businesses leveraging temporary and flexible workers year-round in their operations–up from 57% in 20213. Considering increased turnover and temporary labor, training needs to be simple, repeatable, and quick. The repetitive work of order picking should be easy and engaging in order to increase employee satisfaction, minimize physical strain, and boost productivity.
Faster Cycle Times with Visual Task Allocation
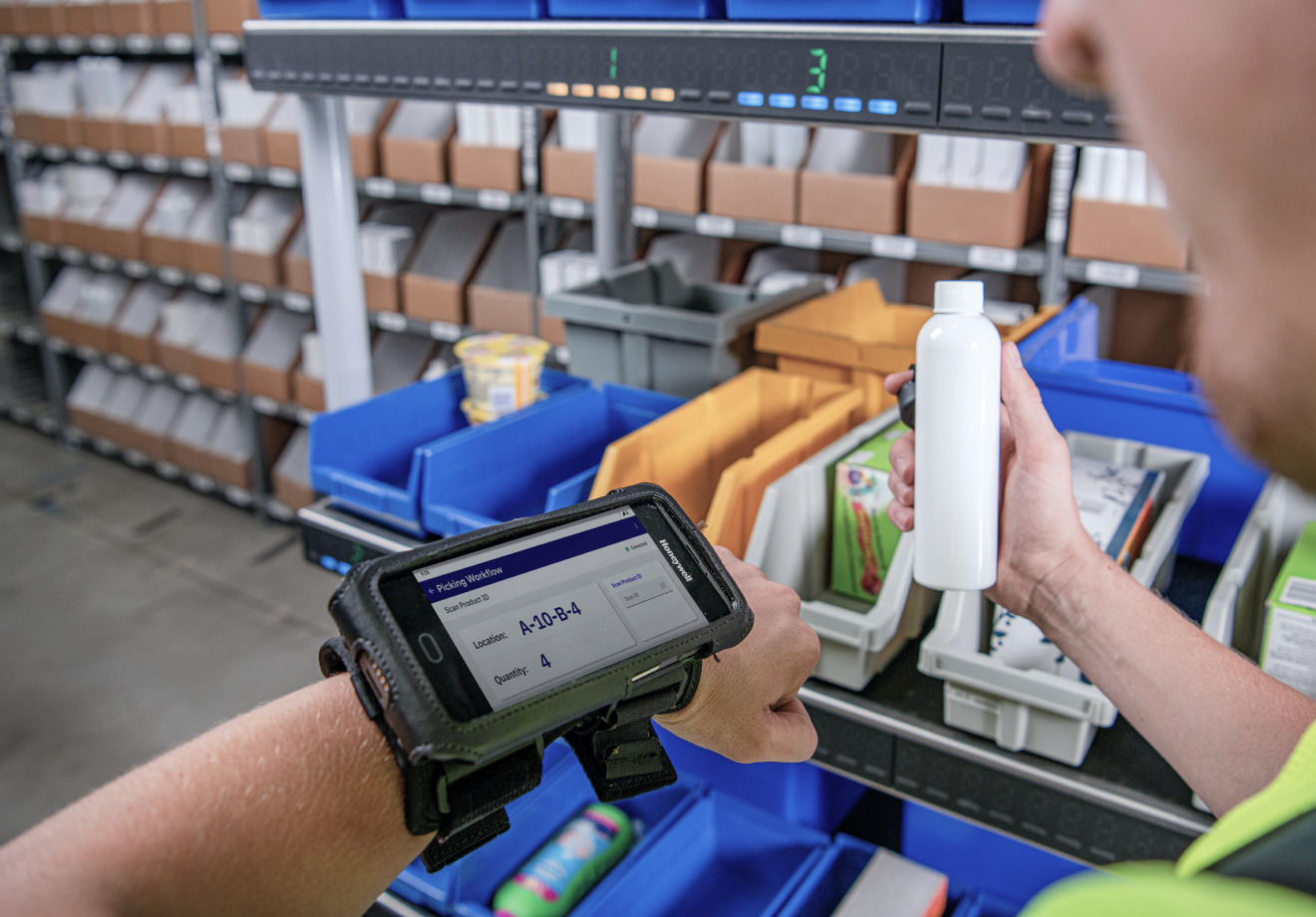
Legacy person-to-goods AMR system offerings rely on a combination of a tablet user interface mounted to the robot and lights on the robot to direct the worker to the proper location, SKU, and quantity for picking. In both “find me” and “follow me” models, pickers need to properly locate their robot counterpart. Once picking, they must determine the proper tote, shelf, and associated quantity for each line item utilizing the user interface and select robot lighting. With our Meet Me™ solution, workers meet their robot at the location specified on their mobile device. They are guided through the pick visually using the Pyxis Point™ user interface. Put-to-light shelving on the Lumabot™️ ensures accurate and simple order picking each time. Workers are informed and enabled, resulting in faster cycle times.
More Capacity, Improved Ergonomics
With over 5% of warehouse workers impacted by work-related injuries and over 2% of cases resulting in days away from work, improving ergonomics with robotic automation can keep pickers happier and more productive.4
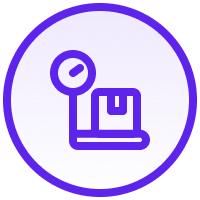
Capacity
Manual order picking typically involves workers pushing heavy carts to complete an order. Current AMR systems offer robotic platforms that can be configured to accommodate different payload dimensions and weight, however, most used in fulfillment have limitations.
Onward Robotics’ Lumabot is capable of handling payloads of up to 460 lb. (209 kg.) with configurable shelving that is wide enough to accommodate larger individual SKUs, taking on the physical labor of moving orders throughout the warehouse.
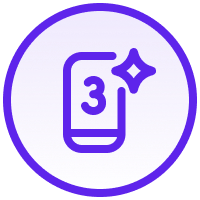
Grab Efficiency
Both the “follow me” and “find me” models utilize a fixed tablet adhered to the robot to communicate the SKU location and quantity to the picker. Onward Robotics’ Pyxis Point mobile application improves pick efficiency and reduces wasted movement for the picker by providing the information they need as they are picking.
Pickers can view the total quantity needed and distribute throughout the assigned totes using patent-pending put-to-light shelving which indicates the proper tote and quantity per tote. Workers are armed with the information they need to pick safely, quickly, and accurately.
With the Pyxis™️ Point mobile application, workers are armed with the information they need to pick safely, quickly, and accurately.
Powered Productivity
Robots don’t take breaks, but just like their human team members, they need energy to perform. Continuous fulfillment relies on robots being fully charged to keep moving product throughout the warehouse. Both “find me” and “follow me” AMR systems utilize power recharging stations. These stations take robots off the floor to power up. Lumabot AMRs use a lithium-ion battery that lasts up to two shifts without a charge and can be hot-swapped during operations, reducing downtime and keeping fulfillment flowing.
Automated Fulfillment is More Accessible Than Ever
When investing resources and time into selecting the right robotics solution for the specific needs of a business, it is important to understand and evaluate a number of factors. Consider which AMR system approach aligns with your KPIs, supports your workforce, and enables your operations to keep up with demand and meet service level agreements (SLAs).
Our unique Meet Me person-to-goods solution revolutionizes fulfillment: reimagining how humans and robots work together by creating a more collaborative, efficient, and flexible fulfillment team. Meet Me increases operational efficiency and eliminates downtime in warehousing, distribution, and fulfillment centers.
To learn how Lumabots combined with Pyxis technology can transform your fulfillment center directly from one of our experts, contact our sales team today!
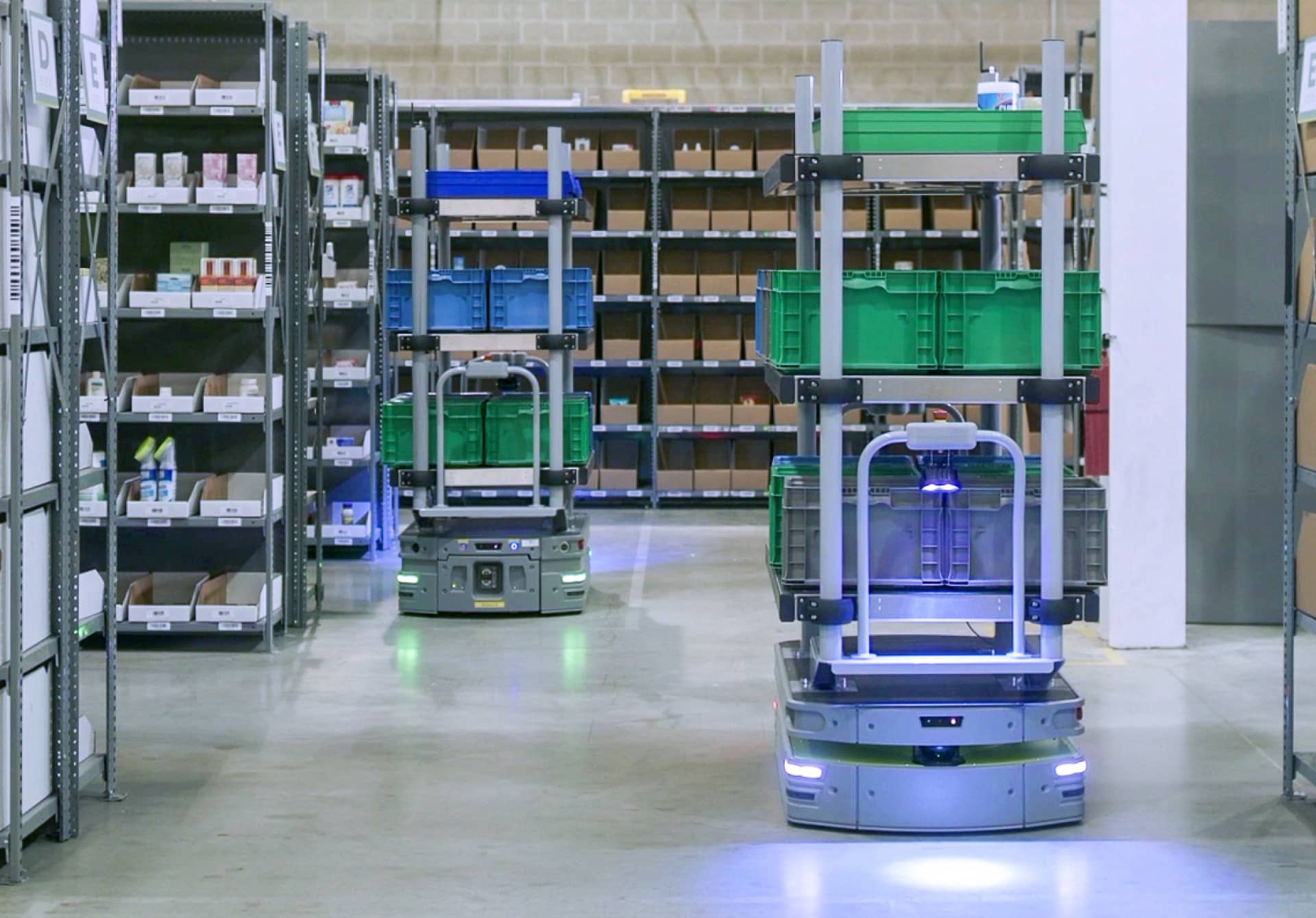
Sources:
- 2023 State of Warehouse Labor Report, Instawork and Logistics Management January 2023
- 2023 Automation Study: Usage & Implementation of Warehouse/DC Automation Solutions, Modern Materials Handling March 2023
- 2023 State of Warehouse Labor Report, Instawork and Logistics Management January 2023
- U.S. Bureau of Labor Statistics 2022